The Future of Industry: Understanding CNC Machined Parts Factory
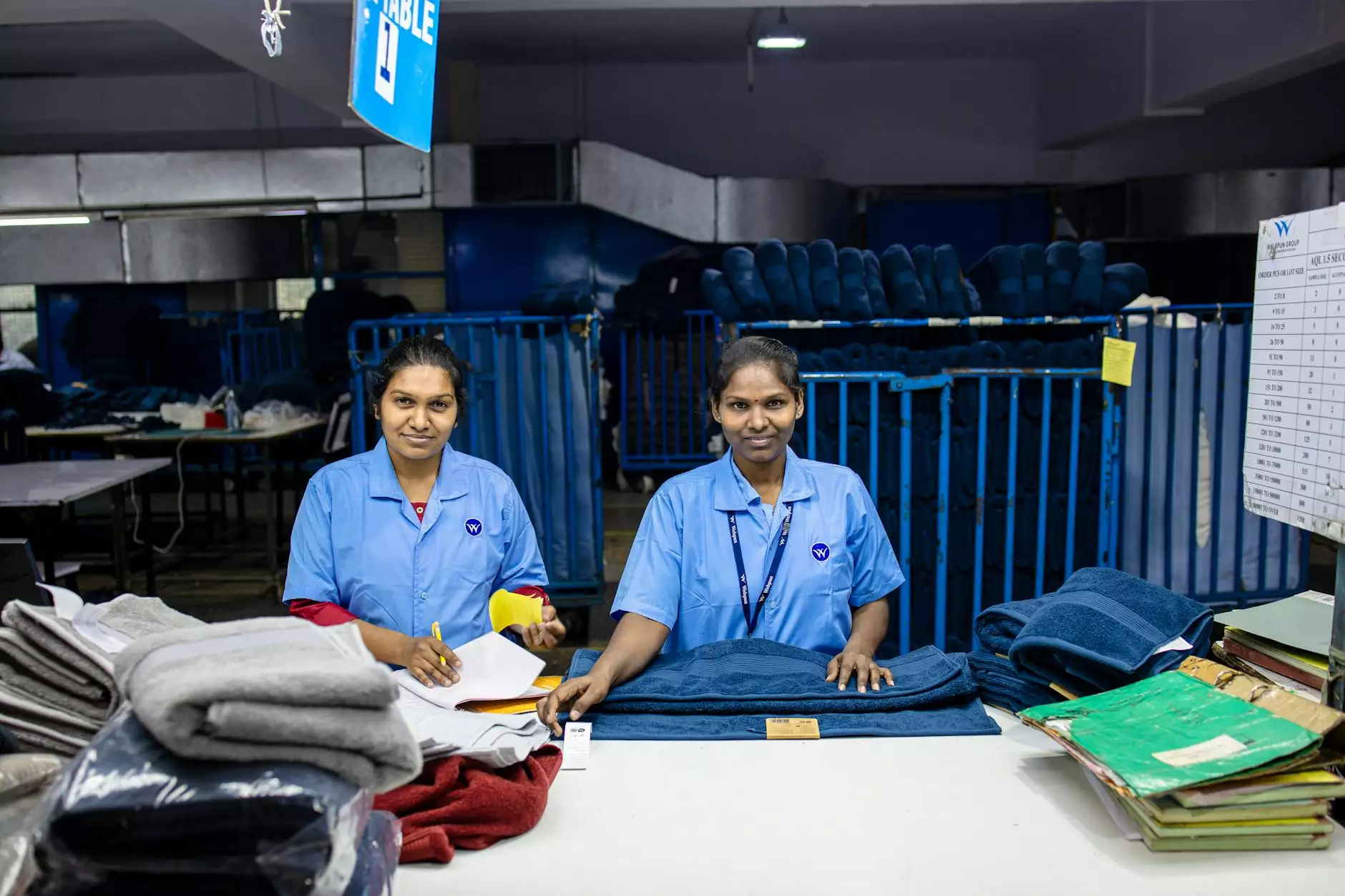
The manufacturing world has evolved tremendously, with CNC machined parts factories leading the charge toward efficiency, precision, and quality. These factories utilize Computer Numerical Control (CNC) technology to produce customized and precise parts for a multitude of industries, including automotive, aerospace, and electronics. Understanding the operations and benefits of a CNC machined parts factory is crucial for tapping into the future of manufacturing.
What Are CNC Machined Parts?
CNC machined parts are components shaped through a highly precise process controlled by computers. This technique involves the use of advanced machinery that interprets a programmed design and executes it through cutting, drilling, milling, and turning operations. Unlike traditional machining, which is manual and often prone to human error, CNC machining ensures unmatched precision and repeatability.
The Process of CNC Machining
The operation of a CNC machined parts factory begins with the design phase. Engineers create detailed computer-aided design (CAD) models of the parts needed. These models are then converted into a machine-readable format, known as G-code, instructing the CNC machine on how to create the part. Here's a detailed breakdown of the CNC machining process:
- Design and Prototyping: Engineers use CAD software to design the part.
- Conversion to G-code: The CAD model is converted into G-code for machine interpretation.
- Material Selection: The appropriate material is chosen based on the specific requirements of the part.
- Machining Operations: The CNC machine executes the program using various tools and processes.
- Quality Assurance: Finished parts undergo rigorous quality control checks to ensure they meet specifications.
Advantages of CNC Machined Parts Factories
Investing in CNC machined parts factories provides numerous advantages that greatly enhance manufacturing capabilities, including:
- Precision: CNC machining offers remarkable precision, minimizing the chances of error.
- Speed: Automated processes significantly reduce production times, enabling manufacturers to meet tight deadlines.
- Scalability: CNC machines can be programmed for large batches, making them suitable for mass production.
- Flexibility: Changes can be made to designs and productions without extensive downtimes.
- Cost-Effectiveness: Although the initial investment in CNC technology can be high, the efficiency and reduced waste lead to long-term savings.
Industries Benefited by CNC Machined Parts
Many industries rely on CNC machined parts factories, including but not limited to:
- Aerospace: The aerospace industry demands high-quality, lightweight, and durable parts, which CNC machining can provide.
- Automotive: Cars require precision-engineered parts, and CNC machining meets these stringent standards.
- Electronics: Components such as housings and connectors must be manufactured with extreme accuracy.
- Medical Devices: CNC machining is crucial in creating components for medical equipment, adhering to strict regulations and safety standards.
- Consumer Products: Many everyday products utilize CNC machined parts for their performance and reliability.
Quality Control in CNC Machining
Quality assurance is paramount in a CNC machined parts factory. Every manufactured part must be tested for accuracy and consistency. Here are some key quality control methods adopted:
- Dimensional Inspection: Each part is measured against specifications using precision tools to ensure they meet the design criteria.
- Functional Testing: Parts may undergo tests to check for their functionality under simulated conditions.
- Material Testing: The raw materials are tested to ensure they meet required standards before the machining process.
- Statistical Process Control: This method monitors the manufacturing process in real-time to identify and rectify issues immediately.
The Future of CNC Machining Technology
The future of CNC machined parts factories is bright, driven by advancements in technology. As industries continue to evolve, here are a few anticipated trends:
- Automation and AI Integration: The incorporation of artificial intelligence will enable smarter manufacturing processes, enhancing efficiency.
- 3D Printing and Hybrid Techniques: The fusion of CNC machining with additive manufacturing will provide even greater design freedom.
- IoT Connectivity: Internet of Things (IoT) technology will allow for real-time monitoring and predictive maintenance of machinery.
- Eco-Friendly Practices: Factories will focus on sustainable processes, utilizing less energy and producing less waste.
- Customization and Personalization: As demand for bespoke solutions rises, CNC machining will adapt to cater to unique specifications.
Choosing the Right CNC Machined Parts Factory
When looking for a CNC machined parts factory, several factors must be considered to ensure your needs are met effectively:
- Experience and Expertise: Look for a factory with a proven track record in the industry.
- Technology Adoption: Ensure they are using the latest CNC machinery and software for optimal performance.
- Quality Control Procedures: Review their quality assurance practices to confirm they meet industry standards.
- Customer Support: Seek suppliers that provide excellent customer service and after-sales support.
- Pricing: While cost is essential, do not compromise on quality; find a balance that supports both.
Conclusion: Embracing Precision with CNC Machined Parts Factories
In the landscape of modern manufacturing, CNC machined parts factories play a pivotal role. The efficiency, precision, and adaptability of CNC machining technology are reshaping how industries operate. As businesses increasingly turn to these factories to streamline processes, reduce costs, and elevate product quality, understanding the intricacies of CNC machining becomes imperative. By selecting the right factory and leveraging state-of-the-art technology, manufacturers can position themselves at the forefront of their respective industries, driving innovation and excellence into the future.