Understanding Precision Plastic Injection Moulding
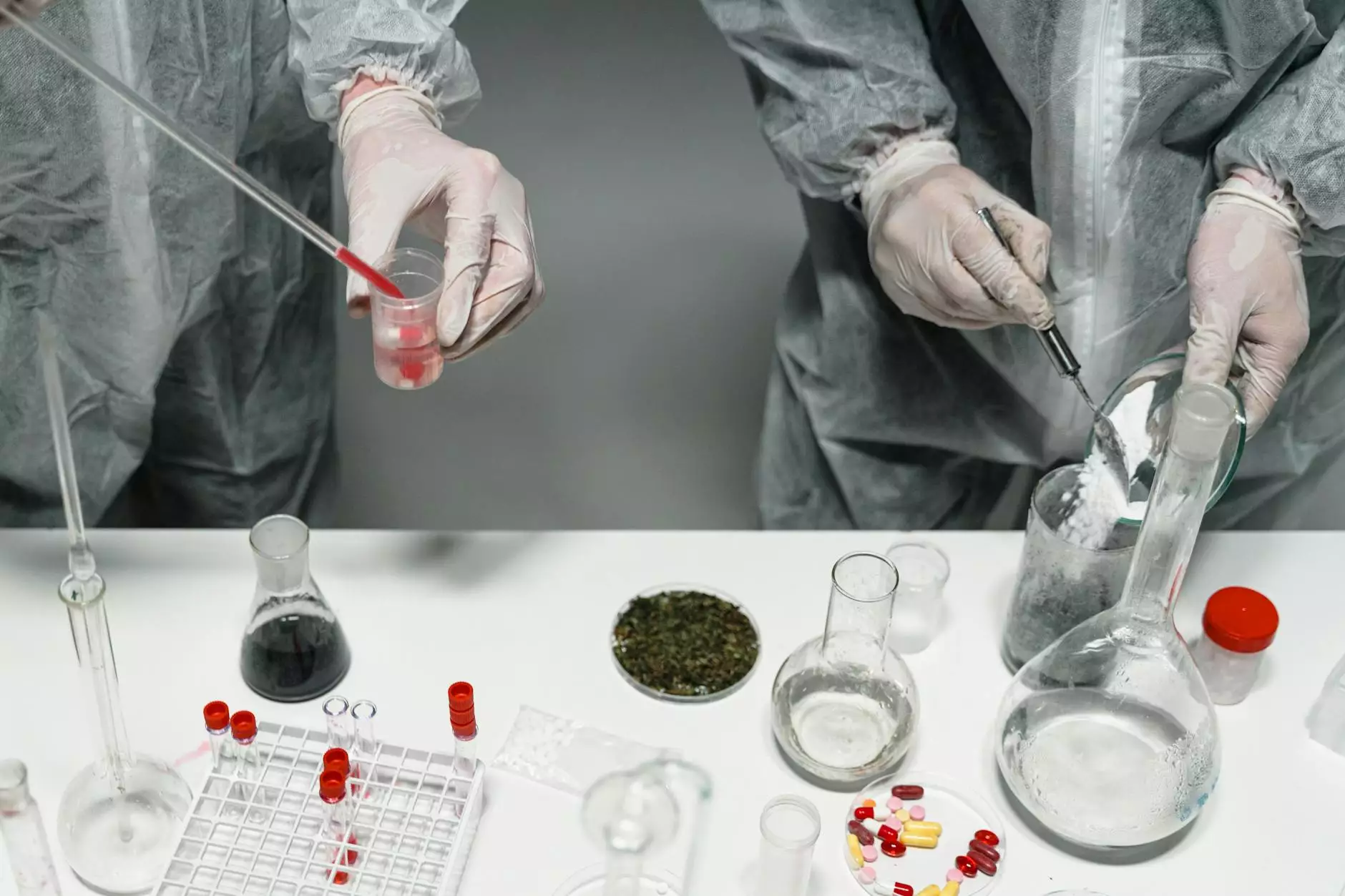
Precision plastic injection moulding is a revolutionary manufacturing process that has transformed how products are made across various industries. This method offers remarkable efficiency, high tolerances, and the ability to produce complex shapes at a relatively low cost. At its core, this technique involves injecting molten plastic into a mould, where it cools and solidifies to form the desired object. The precision aspect ensures that the dimensions and tolerances of the final product are maintained at an exceptionally high standard.
What is Precision Plastic Injection Moulding?
Precision plastic injection moulding is defined as a process where melted plastic is forced into a mould cavity under pressure. As the plastic cools, it takes the shape of the mould, creating a finished product. This method is incredibly versatile and can be used to manufacture a vast array of products, ranging from small components to large parts used in various industries.
The Process of Injection Moulding
The injection moulding process consists of several key stages:
- Material Selection: Choosing the right type of plastic is critical as it affects the final product's properties, cost, and performance.
- Injection: The selected plastic is heated until it becomes molten and then injected into the mould at high pressure.
- Cooling: The molten plastic is allowed to cool and solidify inside the mould, taking its shape.
- Ejection: Once cooled, the finished product is ejected from the mould.
Why Choose Precision Plastic Injection Moulding?
Opting for precision plastic injection moulding offers numerous advantages, making it a preferred manufacturing method in various sectors:
- High Accuracy and Tolerances: This method produces highly accurate parts with tight tolerances, essential for intricate designs in industries like electronics and medical devices.
- Cost-Effective for Large Production: Once the mould is created, producing high volumes of parts becomes cost-effective, driving down per-unit costs.
- A Wide Variety of Materials: Plastic moulding can accommodate various materials, including thermoplastics, thermosets, and elastomers, allowing for tailored properties.
- Complex Geometries: The process can produce complex shapes and designs that would be difficult or impossible with other manufacturing methods.
- Reduced Waste: Precision in the moulding process reduces material waste, promoting sustainability in production.
Applications of Precision Plastic Injection Moulding
The applications of precision plastic injection moulding are vast and diverse. Here are some prominent industries that utilize this technology:
Aerospace and Defense
The aerospace industry demands precision components that can withstand extreme conditions. Precision moulding provides the accuracy and reliability required for aircraft and spacecraft parts, enhancing performance and safety.
Automotive Industry
In the automotive sector, precision plastic injection moulding is essential for producing a range of components, including interior trims, dashboards, and engine components. The lightweight nature of plastic helps improve fuel efficiency, while the precise fit ensures safety and durability.
Electronics
Technology devices require components with precise dimensions for performance and assembly efficiency. From casings to internal parts, precision moulding is integral in the production process of consumer electronics.
Healthcare
The medical field relies heavily on high-precision components, often made through injection moulding. Equipment housings, syringe parts, and even intricate surgical tools can be produced with exceptional accuracy, ensuring compliance with health and safety standards.
The Future of Precision Plastic Injection Moulding
As technology advances, so does the efficacy and capabilities of precision plastic injection moulding. Here are some trends shaping its future:
Increased Automation
Automation in the injection moulding process is on the rise. Enhanced machinery and robotics facilitate faster production times and reduce human error, leading to higher quality outputs.
Sustainable Practices
With increasing awareness of environmental issues, manufacturers are adopting sustainable practices in mould production and material use. Bio-based plastics and closed-loop recycling systems are becoming more prominent.
Smart Manufacturing Technologies
The integration of IoT (Internet of Things) into the moulding process allows for real-time monitoring and data collection. This leads to improved efficiency, predictive maintenance, and enhanced quality control.
Customization
As consumer demand for customized products grows, the ability to deliver bespoke components through precision moulding will become a competitive advantage for manufacturers. This segment is expected to grow significantly in the upcoming years.
Choosing the Right Partner for Precision Plastic Injection Moulding
When it comes to selecting a partner for your precision plastic injection moulding needs, consider the following factors:
- Experience and Expertise: Look for a company with a solid track record and expertise in precision moulding. DeepMould.net, for example, has years of experience in the metal fabrication and plastic injection moulding industries.
- Technical Capabilities: Ensure that the partner has the necessary technical capabilities to handle your project, including advanced machinery and design software.
- Quality Assurance: A robust quality assurance process ensures that every component meets the required specifications and standards.
- Customer Support: A reliable partner offers excellent customer service, helping you through every step of the project from design to production.
Conclusion
In conclusion, precision plastic injection moulding is an essential process in the modern manufacturing landscape, offering extraordinary benefits in efficiency, cost, and versatility. Companies such as DeepMould.net lead the way in the metal fabrication industry, providing high-quality precision moulding services to meet diverse needs across several sectors. As technology continues to evolve, the possibilities within this field will only expand, paving the way for more sophisticated and sustainable manufacturing solutions.